IoT Applications
How does Industrial PLC Gateway BL102 apply to Boiler Monitoring?
Views : 6442
Author : Jeakie
Update time : 2023-06-09 14:19:53
How does Industrial PLC Gateway BL102 apply to Boiler Monitoring?
1. Project background
Boilers are indispensable power equipment in industrial production such as chemical industry, oil refining, and power generation. With the continuous expansion of industrial production scale and continuous innovation of production equipment, the boiler as the power and heat source of the whole plant is also developing towards large capacity, high parameters and high efficiency. Due to the current level of boiler automation control is not high, boilers are mainly inspected manually, but the location of the boiler equipment is scattered, if the inspection and maintenance require the presence of maintenance personnel, it is not only time-consuming and labor-intensive, but also the cost of operation and maintenance is huge. The staff on duty only knew about the failure and reported it by phone, resulting in a delay in dealing with the problem. In order to ensure safe and stable production, the Internet of Things monitoring solution is adopted. Through the Internet of Things, the online real-time monitoring of boilers can realize the remote online collection, monitoring, statistics, analysis and intelligent decision-making of energy saving and emission reduction of boiler operating data, and establish a comprehensive twenty-four for boilers. Hourly monitoring is particularly important.
2. Application Analysis
Boilers are relatively independent, decentralized, and inconvenient to manage
With the large-scale expansion of industrialization, boiler installations are also increasing, but the equipment is relatively vertical, geographically scattered, and even has a large space span, which is not convenient for managers to quickly and effectively monitor and manage each site.
Boiler operation and maintenance service costs are high, and labor costs are large
Offline operation and maintenance services, high travel costs, and high time costs: the reuse rate of equipment service technology is low, no one records and maintains the knowledge of work order operation and maintenance, and cannot view summary reports for repairs, repairs, and inspection records. Unable to objectively assess operation and maintenance personnel.
Unable to understand the operating status of boiler equipment in real time
The state of boiler equipment is uncontrollable to a certain extent, and it is impossible to know the internal operating state of the equipment and the thermal efficiency of the boiler at any time only through manual inspection.
Without remote video monitoring, on-site faults cannot be fed back and dealt with in a timely manner
When the equipment fails, on-site maintenance personnel are required to actively discover the equipment failure, but the automation of the boiler is not high, so the alarm cannot be received in time, and the problem cannot be checked in time, which is time-consuming and laborious.
There is no complete system monitoring data support, lack of scientific analysis and statistical means
Manual alone cannot record a large amount of data in real time, and cannot understand the historical conditions and data of boiler operation.
3.Platform monitoring
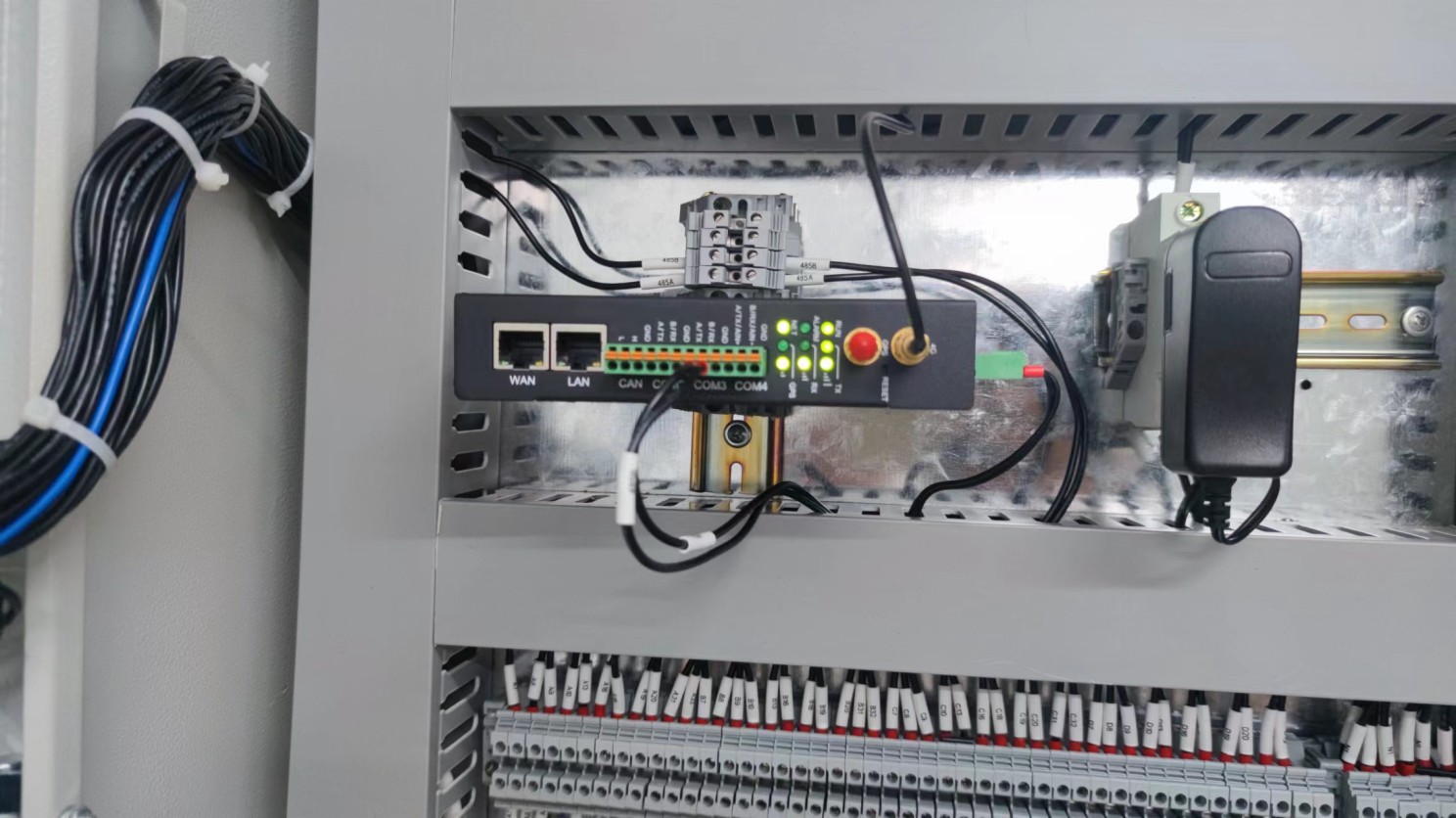
Boilers are indispensable power equipment in industrial production such as chemical industry, oil refining, and power generation. With the continuous expansion of industrial production scale and continuous innovation of production equipment, the boiler as the power and heat source of the whole plant is also developing towards large capacity, high parameters and high efficiency. Due to the current level of boiler automation control is not high, boilers are mainly inspected manually, but the location of the boiler equipment is scattered, if the inspection and maintenance require the presence of maintenance personnel, it is not only time-consuming and labor-intensive, but also the cost of operation and maintenance is huge. The staff on duty only knew about the failure and reported it by phone, resulting in a delay in dealing with the problem. In order to ensure safe and stable production, the Internet of Things monitoring solution is adopted. Through the Internet of Things, the online real-time monitoring of boilers can realize the remote online collection, monitoring, statistics, analysis and intelligent decision-making of energy saving and emission reduction of boiler operating data, and establish a comprehensive twenty-four for boilers. Hourly monitoring is particularly important.
2. Application Analysis
Boilers are relatively independent, decentralized, and inconvenient to manage
With the large-scale expansion of industrialization, boiler installations are also increasing, but the equipment is relatively vertical, geographically scattered, and even has a large space span, which is not convenient for managers to quickly and effectively monitor and manage each site.
Boiler operation and maintenance service costs are high, and labor costs are large
Offline operation and maintenance services, high travel costs, and high time costs: the reuse rate of equipment service technology is low, no one records and maintains the knowledge of work order operation and maintenance, and cannot view summary reports for repairs, repairs, and inspection records. Unable to objectively assess operation and maintenance personnel.
Unable to understand the operating status of boiler equipment in real time
The state of boiler equipment is uncontrollable to a certain extent, and it is impossible to know the internal operating state of the equipment and the thermal efficiency of the boiler at any time only through manual inspection.
Without remote video monitoring, on-site faults cannot be fed back and dealt with in a timely manner
When the equipment fails, on-site maintenance personnel are required to actively discover the equipment failure, but the automation of the boiler is not high, so the alarm cannot be received in time, and the problem cannot be checked in time, which is time-consuming and laborious.
There is no complete system monitoring data support, lack of scientific analysis and statistical means
Manual alone cannot record a large amount of data in real time, and cannot understand the historical conditions and data of boiler operation.
- Remote monitoring of equipment: All parameters of the boiler can be monitored in real time through the web page or mobile APP, including the operating status of the boiler, and the collection of PLC data is supported to make message exchange faster and more convenient, and the same monitoring screen as the scene can be quickly built. Remotely monitor the status of the boiler as if you were on site, which can solve the problems of difficult equipment maintenance, high travel costs, and delays in obtaining information.
- Fault alarm and remote diagnosis: set different thresholds for boiler steam pressure, temperature, flow rate, furnace door temperature, main body exhaust gas temperature, water level and other parameters. If a fault occurs, it will be sent through WeChat message, APP message, and telephone voice at the first time , SMS and other notifications to the management personnel. Real-time understanding of boiler operation through the cloud platform, so that faults can be quickly located and resolved without going to the site.
- Statistical analysis of historical reports: the platform can realize the data summary calculation of multiple boiler equipment, and can carry out intermediate summary variable storage and statistics on boiler furnace pressure, primary return water pressure, outlet water pressure, total steam flow and other data, so as to achieve historical There are traces of data. High-quality reports can make the basic situation of the boiler more transparent and help managers make decisions that are conducive to improving production efficiency.
- Rich user permissions: For convenience, system functions need to be customized according to different users, adding roles with different permissions. Set up different roles to view different menus, add different accounts to view user operation log information, and facilitate the fine-grained management of personnel.
- Operation and maintenance management: users can make equipment inspection plans, and realize equipment repair, maintenance inspection records and other operations on the mobile phone. It can manage the whole life cycle of consumable and core components of the burner, effectively improving the efficiency of after-sales work. Realize that maintenance problems can be checked back and traced to compact operation and maintenance responsibilities.
- Data summary large screen: display the operating status and work data of boiler equipment scattered in different locations in the form of charts, which can be monitored uniformly through computers, mobile phones and large screens. The data display in the form of graphics is more three-dimensional, Can be seen at a glance. Moreover, the graphical display can clearly see the dynamic changes at the first time.
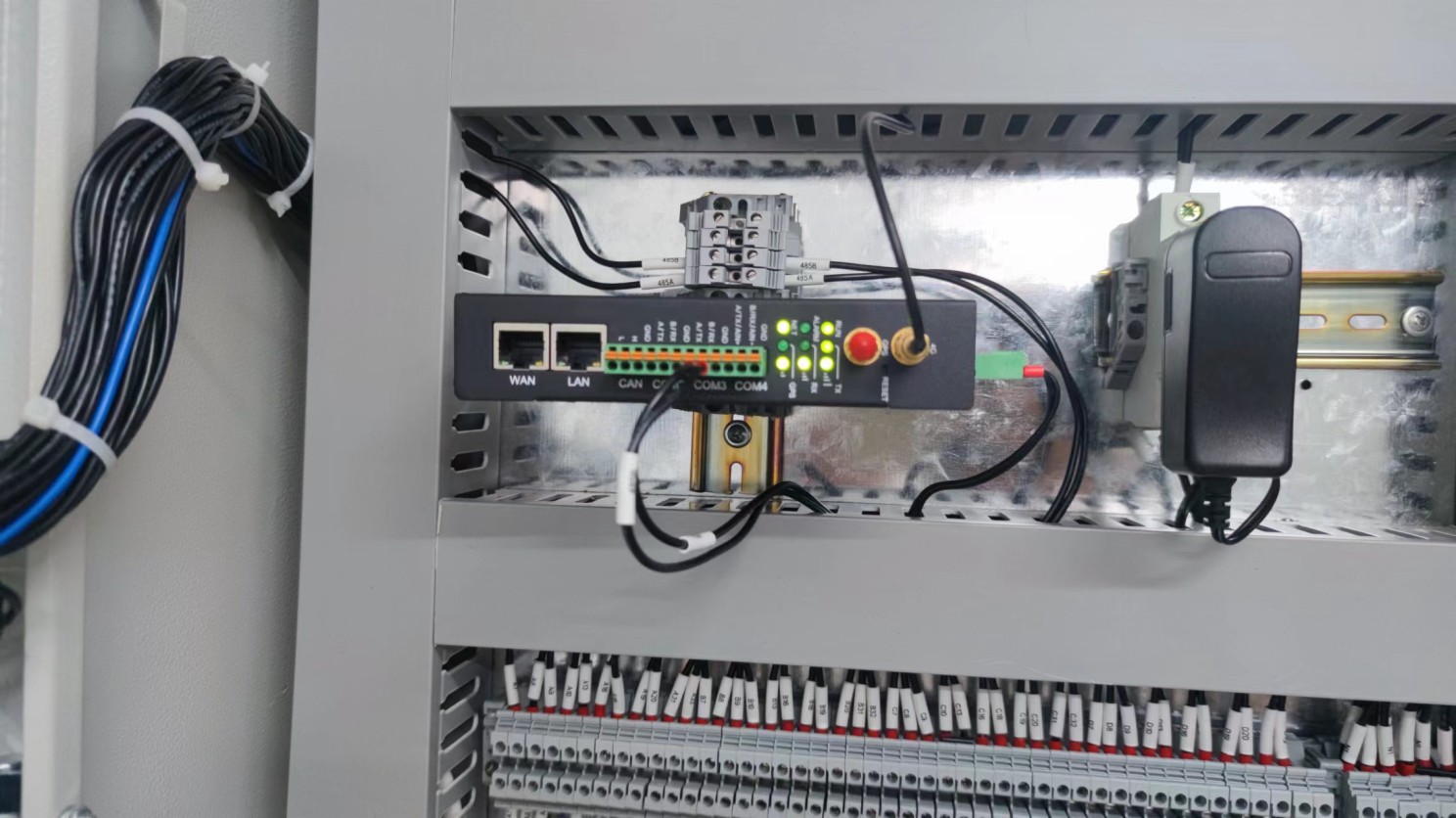
Related News
Read More >>